 
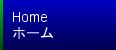 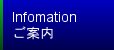 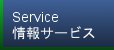 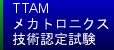 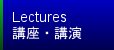 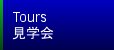 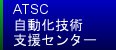
温故知新 自動化アーカイブス 第10回
設計に関する48章から
長期にわたった「設計室」の連載のひとつに「設計に関する48章」がある。自動化に関わる諸先輩がたが後輩に向けて設計の心構えを説いたものだ。ダンボールの奥に眠っていた切抜きを読み返すと、改めて納得することがいくつもある。21回にわたり連載された内容のほんの一部であるが、ここに紹介するとともに、自動化推進のHPにはその全文が掲載されるようにしたい。(渡辺広志)
設計者として貴も重要な要件はアイデアが豊富であることに尽きる。最大公約数的な考え方ではなく、常識を超越した所に前進があり、その時に、設計者の個性が光る。世の中に種々の発想法が氾濫しているが、ここでは考える環境についての提案をしたい。昔から設計の連中は製図板の前で煙草を吸いながら考える振りをしている。下手の考え休むに似たりなのに、などと陰口を叩かれてきた。確かに製図板の前でのみ考えてみても突破口は見つからないのは事実である。そこで考える場所について伝授したい。
1.厠上。
先ずはトイレの中である。アイデアも排泄作業と同じである。有名なロダンの“考える人”もトイレの上での思考を表現したものであると言われている。静かであるし、気分的にも落ち着き、最高の思考環境である。最近は洋式化され、水洗化が普及しているから、多少の時間ならば苦にはならない。トイレに書棚を作る人も多いと聞く。自分が今、解決しなければならない図面でも持ち込んで、じっくり考えてみよう。
2.鞍上。
ここで言う鞍とは、自動車や二輪車のシートの上、又は通勤電車のシートを指す。通勤時間もボンヤリしていないで考えてみよう。自宅から会社までの移動の間の多少の緊張感と、軽い刺激が精神を高揚させ、新しい発想や思考の源泉になり得るのである。又、設計者たる者、十年一日のごとく、毎日同じ通勤ルートに甘んじてはならない。時にはルートを変えてみよう。別の視界、異質な感覚が、別の発想を生むかも知れない。
3.枕上。
さて、厠上、鞍上、でも良いアイデアが出ない人は枕上で考えてみよう。アイデアの「条件反射説」がある。梅ぼしがすっぱいことを経験的に知っている日本人は、梅ぼしを見ただけでツバが出る。これが「条件反射」である。反復刺激が神経の新回路をつくることが理論づけられている。人間の脳は1,400グラムで体重の2%にすぎないが、体内の15%の酸素を消費する。そして20歳をすぎると、1日あたり10万個の脳細胞が死滅し、1年1グラムの割合で脳は軽くなる。反復刺激で新しい神経回路をつくり(これを神経細胞の発芽と呼ぶ)アイデアを出すしくみを脳内に作ろう。生きている人間の脳は超低電圧の微弱な生体電流=脳波がながれている。この脳波には、α、β、θ、δ波の4種が典型的であり、α波(8〜13ヘルツ、20〜50マイクロボルト)の時にはよく記憶し、よく想い出す性質を持っている。個人差もあるが、就寝して入眠までの30〜60分と朝の眼ざめ時の30〜60分がα波活用のチャンスである。枕元に、メモ帳を置き、浮んだアイデアをメモする習慣をつけよう。以上、アイデアは3上(厠上、鞍上、枕上)から、の教訓を生かして、キラリと光る個性的な設計者になって頂きたい。
せ 設備設計の4原則
1.作る人の身になって設計せよ。
2.組立てる人の身になって設計せよ。
3.使う人の身になって設計せよ。
4.保守する人の身になって設計せよ。
設備設計は設計者の個人的な好みで設備作りをしてはならない。必ず上記の4原則を守って設計をすれば名設計者になれる。設備メーカーは別として、各会社の生産技術や、工機部門で設備設計を担当すると、製作から廃却に至るまでの設備の一生涯(ライフ・サイクル)の面倒を見る場合が多い。従って、各部門からの苦情を全て背負い込む立場にある。逆に各部門からの名声を得る立場でもある。どちらを選択するかはこの4原則を守るか否かで決まる。
1.作る人の身になれ。
図1を見て頂きたい。若い設計者が犯しやすい図面である。丸物部品図を書く場合には、旋盤なり、研削盤の作業者が、どんな風に切削をするのか、要するに、どこをチャックして、どこから寸法を、どんな検査具を使って測定するのか、熱処理がある場合にはどの程度の変形が予想されるのか等を考えながら設計することが望ましい。
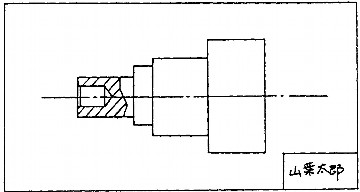 【図1】
2.組立てる人の身になれ。
加工はできたが、組立ができないミスをする場合がある。現場からどうやって組立てるのか、教えてくれ、とどなり込まれ、オロオロする場面が見られる。どんな順序で、どこを基準に組立てるのか、どんな工具を使って組立てるのか、’組立工具を入れるスペースはあるのか、芯出しはどうするのか等をよく考えたい。検図者の最重要チェックポイントでもある。
3.使う人の身になれ。
治工具設計の名人のやり方を見ていると、先ず現場でその作業をジーと見ている。そして、自分でその作業をやってみる。作業のポイントを自分自身で押えるのである。そして作られてきた治工具を自分で使ってみてから作業者へ渡し、不具合を聞いて修正してやる。その名人が設計した治工具で捨てられた物は一つもない。
4.保守する人の身になれ。
ベアリング1個を交換する為に、機械の大部分を分解しなければならないとか、ベアリングを取り外す考慮がされていない為、サンダーやタガネで見るも無残な姿になってしまう場面を見ることがある。その為に何時間も生産を止めて混乱を招き、設計者の面目丸潰れである。MP(Maintena-nce, Prevention:保全予防)設計を心掛けたい。
か 改善の4原則,E,C,R,S
IE(インダストリアル、エンジニアリング、Industrial, Engineering)の手法の中に改善の4原則という原則がある。作業改善によく使われる手法であるが、自動機設計にも当然応用できる。この一般的手順は、機械全体をある細かさに分割し、それぞれにこの4原則を通用してみる。こうすることによって改善のヒントが得やすい。
1.排除(やめられないか?)、Eliminate
2.組合わせ(他との組合わせ)、Combine
3.入替え(他のアイデアとの入替え)、Rearrange
4.簡素化(単純化できないか)、Simplify
この4原則の適用はE, C, R, Sの順序で行うことが重要である。つまり最も重要なアプローチは、排除である。
1.排除
機構の中に排除できるものはないか。それは何のためにあるのか。その目的は何か?。その目的自体を不要にするアイデアはないか、を見つける。他の検討に先立って、まず「排除」の可能性を徹底的に追求する。この排除が実現すれば、その改善効果は他の3つの原則より大きい。
2.組合わせ
別な機構との組合わせによって新しい着想が生まれることがある。カム機構に固執しないで、カム機構とエアー機器との組合わせや、エレクトロニクスとの組合わせ等により、より信頼性の高い機械を設計出来る場合が多い。エアー機器メーカーだから全空圧制御とし、カムも電気も使わないラインを作ろう、などと発想するのは多少無理があり、適材適所の機構を使えばよいと思うのである。自動組立のシステムを作る場合には、ある作業と別の作業、または一連の作業を一緒にできないか、2プラス2が3となるように、組合わせた方が短い時間にならないか、などを考えてみる。
3.入替え
工程の順序を入替えることにより改善できないか、別の機構と入替えることにより、更に良くならないか、と考えてみる。
4.簡素化
以上の3つの原則の適用を試みた後で、最終的に簡素化に踏み切ろう。と言うより、以上の3つの原則を適用すれば必然的に簡素化されると考えてもよい。
この改善の4原則を適用する時は、科学的態度、すなわち意識的、疑問的態度で臨み、すべての分析が終えるまでは、現方法のどんな事柄も必然的、不可避な事である、と受け入れることなく考察をすすめてみることが大切である。
「自動化推進」87−4
執筆者…………編集委員会・設計室グループ
●本号執筆者:塩沢 晃
ヤマハ発動機叶サ造事業部生産技術部課長
構想は設備開発のステップで非常に重要なステージである。なぜなら、構想以上の機械は出来ないのが常で、構想通り実現できれば満点であるからである。この意味で構想は、実現するべく機械の完成予想図であり、このステージで、重要な仕様はほとんど決まってしまう、のである。若手設計者の構想図を見て、がっかりさせられることがよくある。形は不格好で大きく、なにしろ構造が複雑である。こんな図面を、「構想が出来ました。見て下さい。」と持って来られても「よし、これで行こう。」なんて言葉は、出る訳はないし、この設計者には期待しているのに、こんな程度では先が思いやられる。別な職種でも見っけてやらねば……とか、とんでもない方向に気持ちが沈んで行く。
この様な場合は、大体がアイデアの少ない構想図である。つまり、自分の持つ現実の中だけで構想をたてているのである。構想は夢である。創造力をもって、もっと大胆に夢を表現してもらいたい。一方では、現実を無視し構想図でなく、妄想図になっているケースもある。“大丈夫ですよ課長、製品設計を直してもらいますから”とか“アポロでもやっていますよ、テレビで見ましたから”現実におぼれず、妄想に走らず、である。構想は夢をもってやってもらいたい。しかも正夢として実現しなければいけないことを忘れずに、構想設計のステージは「よし!これで行こう」としめたいものだ。
ひ 広く大きい所からはじめよ
構想設計のやり方について、であるが、大枠のレイアウトなり、仕様決めなどから入って行くのが通常であり、そんなことは言われなくてもわかっていると言われるでしょうが、えてして、逆の詳細構想から組み立てた構想図をよく見る“この操作パネルは使い勝手が悪いから、ここに持ってこれないかね”“課長、そんなことはわかってますよ。でもここは、この機構がはみ出しているから、だめですよ。ここしかないんです”又“機械がこんなに大きくては、構想のやり直しだな。大体、設置する時、工場の壁をぶち破らなければ入れられないよ”“課長、しょうがないですよ。このメカニズムが必要なんですから。大きさなんて何とかなりますよ。動けばいいんですから”“そんなことはないよ。このメカニズムの向きを変えるとか、別なこんな方法でも使えば、半分の大きさでいけるじゃないか、ね”“でも………”よくある会話である。狭く、小さい所の部分構想から積み上げると、どうしてもこの様になる。構想設計は、アウトラインから出来るだけ広い目で見て、大きい所から始め、枠決めの中で詳細構想に入って行くのが、順序である。
も 目的忘れて手段が走る
VE手法の機能展開を思い出してほしい。電気の配線がある「なんのために?」(モータに)電気を流す必要があるから。「何のために?」カム軸を回転する必要があるから。「何のために?」レバーを揺動する必要があるから。「何のために?」パレットを移動する必要があるから。「何のために?」………
結局目的は、部品を組むことである。パレット、レバー、カム軸、モータは手段である。手段は選択であって、もちろん、上記が誤っているとは言わないが、ここで言いたいのは、一つの目的で手段は無限にある。ややもすると、手段が目的であるかのような錯覚に落ち入り、知らず知らずのうちにパレットやカム軸が固定化して、特に何か状況が変わった時など、手段だけ走ってしまい“カム軸でピッチ切換をするんだから、時間が掛って当然だよ。とか“パレットを交換するんだから、パレット乗せ換え装置は必要であって無駄ではないよ”と言うような事になる。パレット自体が無駄かも知れないのに………。目的を忘れると、手段だけが走り使いづらい、高い機械ができてしまうのである。
さ 三分の新規に七分の類似
若手設計者の中には、何でも自分流に工夫をこらし新規設計しないと気がおさまらない人が多いと思います。しかし、結果として設計はなかなか終わらないし、工事が始まれば期間は長く掛るし、あっちこっちでトラブリ、工事が終了するまでつきっきりで、次の開発に手が回らない状態が目に浮かびます。早く一人前になろうとしての行動が、次のチャンスを棒に振って結局損をする結果となります。全く新規に開発した所はベテランでもよくトラブリます。ですから、ベテランは工夫するべき所、工夫をしなくても良い所、又は、危険を犯してもチャレンジする所、危険を犯さなくて安全に行く所等を、構想段階で区分けします。社設備開発の場合では、同じものを何回も設計することは滅多にありませんが、メカニズムで考えれば類似のものが沢山あるはずです。全く新規の開発テーマであっても、多くて3割の新規設計にとどめ、7割は先人のメカニズムを、そのまま編集するのがコツです。3割が1割ですめば、成功まちがいありません。
「自動化推進」87−5
執筆者…………編集委員会・設計室グループ
●本号執筆者:西郷達治
セイコー電子工業叶カ産技術部製造試作課課長
工作機械の主要構造には鋳物が多い。しかし一品料理的専用機械・装置においては特に最近、鋳物が使われないで溶接構造が用いられることが多い。
鋳物にするか溶接構造にするかという判断も、製作台数による損益分岐点が少し前だと数台であったのが、景近では10数台とも云われ、よけいに使われにくくなってきている。それだけ溶接加工法がNC化などによって作業性向上があったと考えられるし、鋳物では木型というコストを除いても作業環境のダーティさも手伝ってさらわれる傾向になるのだろう。
機械製造の工程はまず木型作製から始まる。寸法抜けなどが木型屋からの指摘で助かったことも何度かある。そんなとき、
「俺達ちゃお前らの図面の検図やってんじゃねえゼ」
などと云われたものである。
或る日その木型屋から木型が完成したから、チェックに来いとの連絡を受けたので、木工室へ出かけ、持参した長尺の物差を使ってチェックを始めた。
ところがどこを測ってもどうも寸法がおかしい。恐る恐る親方に申告したのであるが、大声でどなり飛ばされた。
「鋳物は煮えれば、冷えるんだ!!」
鋳物尺でこっぴどく尻を叩かれたのである。なんたることか膨張系数を忘れて普通の物差で測っていた。
別の日、鋳鉄部品の剛性が不足していてどうしても撓みが予測を越えて、精度が維持できないことがあった。若きエンジニアは「ようしそれなら鋳鋼に変えよう。」と云ったのだが、結果的にこれも机上論でしかなく、またまた叱られたのは云うまでもない。
アルミ鋳物を鋳鉄に変えることはよもや考えもしなかったろうが、縮みしろ鋳鉄一般0.8%、鋳鋼1.6%をすっかり忘れていたのである。(注1)
(注1) 鋳物尺の割合
縮みしろ | 使 用 個 所 |
---|
0.8% | 鋳鉄一般
| 1.2% | アルミニウム、一般青銅
| 1.4% | 高力黄銅、鋳鋼
| 1.6% | 鋳鋼(肉厚10mm以上)一般
|
し シンプル イズ ベスト
おおよそ自分の回りを見てみると設計屋には二つのタイプがある。
設計仕様書などの解読が充分行なわれ、技術計算なども済ませ、自分がこれから設計しようとするテーマの目的がはっきりしてドラフターに向ってからの話しに移る。
A1程度のセクションペーパーに、中心付近にポッツリと機構図を浮び上らせ、それがだんだん周囲に拡がって行くように進めていくタイプ。若干の補助投影を別にすれば一面のみの組立図をみごとに完成させ、次にこれに対応した側面図なり平面図なりを仕上げて行く。
この設計者はかなり緻密な構成が頭のなかでおこなわれていてそれを表現できる能力の持主で、天才タイプである。
もう一つは、セクションペーパー全面のいたる場所におよそ第三者が見たのでは理解できないようなプロット的組立図を出現させ、それをやがて見事に関連づけて一枚の設計図に完成させていくという手法の持主である。
前者が「必要スペース積上的ミニマム設計」の手法と呼ぶとすれば、後者は「外枠決定的スペ一スセービング設計」と呼んでもよいだろうか。
どちらが良くてどちらが悪いという答は特に出すつもりは無いが、これには設計者の性格的な要素もあるのでテーマの内容によって配分すれば特色を出し、それぞれの長所を生かすことができる。問題はその中味である。
元来当初構想する機構はシンプルであったはずであるのだが、加工精度上の心配や組立調整のやり易さなどの条件を考慮しながら部品点数が増えていくのが普通であるべきだ。
しかし稚拙であるが由に闇曇に最初から複雑な構造設計をしてはばからぬ設計者が居る。こんな設計者は配置転換願をした方が良い。
加工機がどのくらいの精度で部品を仕上げられるか理解できないままに、或は設計製作される機械がどんな手順で組み立てられるか考えも無しの所産であるということができる。
少い部品で目的を達成するということは、コストセービングばかりでなく.故障、信頼性、メンテナンス性も含めて高パフオーセンスであるのは昔から論を待たない。
部品を1点1点描きながらその部品の機能や目的を考え、本当にその部品がどうして必要であるのか、省略できない部品なのか念仏のごとく自問自答しながら設計を進めるべきである。
単純は複雑にまさる!!と云える。
は はずみ車は生きている
何故カウンタープーリーと呼ばずに「はずみ車」と云うか理解願いたい。
すでに無人稼動に近い自動盤でさえも、二昔、三昔では大半が建屋ごとに天井設置されたカウンター軸のはずみ車からベルト掛けであった。細いスピンドルなどは木綿の水糸(みずいと)でドライブされていた時代もある。電動機がまだ貴重品だったのだろう。
その様な、増産につぐ増産で社内が手狭になり、次々と協力工場を建設していくと云う時期にあたって、当然これらの自動盤も移転の運命にさらされることになる。しかしこのタイミングで古色一掃「どうせ移転させるなら」という理由で木製台に並べてカウンター掛けの自動盤は独立した鉄製の脚に置き替られ専用モーターで運転することになった。
脚も当時ではめずらしく鈑金構造で作った。
主軸に必要な回転数はこれこれであるから、電動機の回転数にこの比率を掛け算してプーリー径を決定した。しかし電動機プーリー径がやたらに大き過ぎてどうも恰好が悪いので数値合せのため電動機は2ポールにしてプーリー径を約2分の1
に修正して設計を終えた。
時がたって或る日現場からの呼び出しで、大目玉を喰った。曰く、〈バイトが最大切削負荷時にスピンドルの速度が落ちる〉、というのである。
青くなって飛んで行ったがなるほど嘘ではない。ベルトがスリップしていないか?テンションが弱過ぎないか?など調整したり、ベルトワックスを塗布したりしたが決定的な改善には至らなかった。
改めて元の天井にあったはずみ車の威大きを知らされたのである。怨めしきかなGD2。形而下にとらわれ「仏作って魂入れず」とはこの事であろうか。
モーターを6ポールまで落して、あざ笑われているように大きな駆動プーリーを採用したことは忘れられない。済んだことにも宝の山あり。
「自動化推進」87−6
執筆者…………編集委員会・設計室グループ
●本号執筆者:本田 保宏
(アトリエ・じゅん主宰)
前へ 次へ
|