 
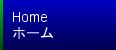 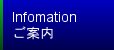 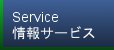 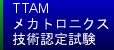 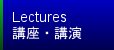 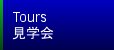 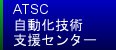
温故知新 自動化アーカイブス 第2回
会報委員 渡辺 広志
株式会社東京自働機械製作所
記事名:カム機構設計の要点(その2)
執筆者:牧野 洋(山梨大学工学部)
掲載号:自動組立ニュース1973.2〜1973.7(全6回)
(前号よりつづき)
4.カム曲線は何がよいか
カム曲線に何を使ったらよいかと言う質問に、もし正確に答えるとすると次のようになる。
「それは負荷の性質と用途によって異なり、それぞれの目的に応じた曲線を選択しなければなりません。」
だが、これでは、首相の国会答弁のようにそっけない。そこで、本誌の読者だけに特別大サービス、これ一つだけ知っていればまずどこに使っても大丈夫だというカム曲線をお教えしよう。それは変形正弦曲線(Modified Sine Curve)である。
変形正弦曲線の変位S、速度V、加速度A、躍動Jを図1に示した(−図省略−)。S、V、Aはいずれも連続であって、このことは、この曲線が高速に耐えることを示している。しかも速度の最大値Vmは1.76と低く、サイクロイド曲線や変形台形曲線のVm=2.00に比べると、それだけカムを小さくできることになる。
Vmの小さいことは重不可に耐えることを示すし、Amも、変形台形曲線よりは大きいが、サイクロイドよりは小さい。トルク特性がまたなめらかで、他の曲線のように鋭い山がない(トルクは大体においてV×Aの形できくと考えてよい)。
大体、カム曲線を「作って」みたことのある人なら知っていることだが、何もかも満点の曲線というものはない。Vmを低く押えようとするとAmやJmが高くなり、Jmを押えればAmやVmが上り、Amを押えればVmやJmが飛出す。ゴム袋を押え込む感じなのである。そうして、理屈の上ではJmやAmの小さい方が振動に対してはよく、Vmの小さい方が重負荷に対してはよく・・・・・・となるのだが、現実の問題ではこれらが複雑に絡み合っており、本当のところ、どれがよいのかは分りはしない。
先年も、あるカムの講習会で、例によって「高速軽荷重には変形台形曲線が、中低速重荷重には変形正弦曲線あたりがいいでしょう」と話していますと、聴講生の中から質問が出た。「先生、重荷重というのは何kgぐらいで、高速というのは何rpmのことですか」これには参った。そんなに明確に区別できるものではない。現物を見れば曲線が何が良いかはおよその見当はつくが、何kgと言うだけでは条件が不足なのである。そこで「まずどっちかで作ってみて、それで駄目なら他の曲線に変えるのですね」と言う、まことに乱暴なことになってしまうのである。
実際のところ、こういう因子が数多くあって、それぞれの因子が複雑に絡み合っている問題では、最終的な良否の判断はフィールドテストに頼るしかない。実際に使ってみて、どれがよかったという結果、それも、たった一つのデータではなく、多数の会社の、多数の用例の結果によって、総合的に判断をするようにしなければならない。
ローラギヤ方式のインデックスユニットを作っているファーガソン社(Ferguson Machine Co.)を訪れたときにも、私にはこのことが頭にあった。この会社は、おそらくインデックスユニットを世界で一番数多く作っている。この会社で聞けば、カム曲線は何がよいかについて少なくとも、インデックスユニット用のカム曲線は何がよいかについて明確な答えが得られるに違いない。
セールスエンジニアのM.C. Riegert氏は慎重に答えた。「私個人の考えでは変形正弦曲線が一番優れているのではないかと思います。テーブルの動きが、他の曲線の場合に比較して、なめらかなような気がするのです。」
それから2年後、ファーガソン社は、カム曲線の標準をそれまでの変形正弦曲線と変形台形曲線の2本立から、変形正弦曲線だけに変更した。
5.ガッチリとスッキリ
カムを使った機械系をどのように設計したら良いかという問題は「ガッチリ」と「スッキリ」という二つの言葉に要約できると思う。すなわち、カムより前はできるだけガッチリと、カムよりあとはできるだけスッキリと設計することが必要である。
ここでカムより前といっているのは、電動機からカムに至るまでの駆動系のことである。この部分の一般的な構成を示すと下図のようになる。
この部分の各機構要素は十分に負荷に余裕のあるものを用い、ガタやタワミのないものにしなければならない。
まず、電動機は十分に馬力のあるものを用いる。計算上400Wが必要であれば750Wを用い、750Wが必要であれば1.5kWを用いる。電動機のイナーシャは大きすぎるぐらいの方が良い。プリントモータのようなきゃしゃなものはいけない。カム軸のトルク変動は他の負荷に比べて大きいので、容量の小さなモータだと振りまわされて回転ムラがでる。これを防ぐためにフライホイールを入れることは効果があり、電動機の容量を小さくすることができる。
VベルトとVプーリの部分にはそれほど問題はない。しかし、テンションを十分にかけてベルトのたわみをなくすことと、Vプーリと軸との締結に当ってガタのない機構にすることが必要である。キーのはめあいは十分に固いものを用いる。タイミングベルトの使用はすすめられる。
減速機はバックラッシュのないものを採用すること。平歯車減速機は負荷側から入力側をドライブできるのでのぞましくなく、ウォーム減速機が良い。スピロイド減速機(園池製作所)のような、バックラッシュの調節できる減速機がのぞましい。
一番問題なのはカップリングである。心合わせを容易にするためにゴム継手などのたわみ軸継手を用いることが多いが、これが振動を起す原因になる。ペンディックス継手のように、トルク方向に対する剛性が大きく、曲げ方向に対する剛性の小さいものが良い。最近、新しい構造の継手が多数開発されているので、これらのうちから目的に適したものを選択するようにする。一番良いのはカップリングをなくし、減速機とカム軸を直結にすることである。
カム軸の径は一般に細すぎる。高速をめざすほどカム軸は太くしなければならない。長手方向が1mクラスの自動組立機械ならカム軸の太さは少なくとも35mm、5mクラスの組立機械なら50mmにはする必要があるだろう。これは強度の問題ではなく剛性の問題である。カム軸のねじり振動は最も警戒するべきなのだ。
カム軸とカムとの連結にキーがのぞましくないことはすでに述べた。これも一番良い方法はウォームホイールを直接カムに貼り付け、軸を経由せずにトルクを伝達することである。
以上述べたように、カムより前はできるだけガッチリと構成する。組み上げた状態で(あるいは想像で)カムに左まわりにある大きさのトルクをかけ、次に右まわりにトルクをかけてみて、その間でカムが角度にして数度も回転する(バックラッシュがある)ようなら、そのカム装置は落第である。
一方、カムよりあとはできるだけスッキリと構成する。従節ローラから従節の動作端までできるだけ軽く、しかしながら十分な剛性を持つように設計する。従節系の大きさはなるべく小さくコンパクトにまとめ、質量を小さくする。できうるならば、カムを従節作動端に近付ける。自動車のオーバーヘッドカム(OHC)を想起していただきたい(図1参照)
従節リンク系の各リンクはできるだけ薄く、しかし、力のかかる方向には幅をとり、適当なリブをつけて、ペナペナしないようにする。

従節ローラをカムに押し付けるのにはばねを使うのが普通であるが、このばねは十分に強いばねにする必要がある。押し付ける力を静的な状態だけで判断して決めてしまうことが多いが、動的な負荷のかかることを忘れてはいけない。正しい設計法としては、最高回転数における負の最大加速度を求め(これはカム曲線がわかれば、それから求められる)、ローラ部(あるいは、ばね取付け部)における等価質量から最大の慣性力を求めて、それに打ち勝つ程度の強いばねにする。これは従節の浮き上りを防ぐためである。
ばねは強いだけでなく、こわくなければならない。これは従節系の固有振動数を高めるためである。運動部のマスを軽くし、k(ばね定数)を大きくする。これは高速化における一つの要件である。
ばねを使う代わりにエヤシリンダを用いて従節ローラをカムに押し付ける方法があり、ギルマン社などが採用している。これも好ましい方法である。
(記事ここまで)
この記事が書かれてからすでに30年。自動組立機械の寿命を10年と見積もっても3世代が過ぎた。当時に比べ、カムで仕事をする機械の割合は確実に少なくなっている。特別な用途以外ではその座をサーボモータとエヤシリンダに奪われたといっても過言ではないだろう。かくいう私が勤める会社でも、カム式の機械の多くは”多軸サーボ+エヤシリンダ”の制御にとってかわられた。
ではカムに憧れても設計する機会に恵まれない今の技術者にとって、この記事は単なる昔話、ノスタルジアを伝えるだけだろうか。私にはそうは思えない。
記事の中にあるとおり、カムは確動機構である。裏を返せばカムが確実に動作するように機械系を設計しないことには満足に動作しないのである。機械の出来・不出来が分りやすいのだ。
対してサーボモータは理想的なパルス列を与えてもそのとおりに動くとは限らない。立ち上げ時にはモーションコントローラによるモータのチューニング(追従性向上のための定数設定)作業が不可欠であり、これが適切に行なわれて初めて与えるパルス列に意味が出てくる。しかし1パルスの狂いもなくモーターが追従することは現実不可能であるから、与えたパルス列に対してある幅を持って追従すればよしとする。この幅を大きく設定すれば機械系が少々まずい設計でも動いてしまう。エヤシリンダに至っては速度調整はたいていの場合スピードコントローラによる排気制御。仮りに圧縮空気の供給量が足りなくなり元圧が下がっても、そのうち動作は完了する。機械の不出来のかなりの部分が制御側でごまかし可能であり、自然と機械の完成度は低くなる。
以下の事例に心当たりがあるのなら、自らの設計を見直す必要があるだろう。
・アクチュエータ同士がその動作範囲内で干渉するが、ソフトのシーケンスを工夫することで衝突を避けている。
・衝突時にはモーションコントローラに付属する過負荷(オーバートルク)感知機能で止まるはずなので、特に過負荷保護機構は考慮していない。
・ワークの先走り防止目的のスプリングロードがあちこちにある。
・ベルト・チェーン等をサーボモータで駆動した際の伸び・ガタ対策として、センサによる停止位置確認・サーボによる補正をしている。
ちなみにこれらの事例は、今私が手がけている機械において該当するものばかりである。
前へ | 次へ
|